The Role of CNC Lathe Factories in Modern Metal Fabrication
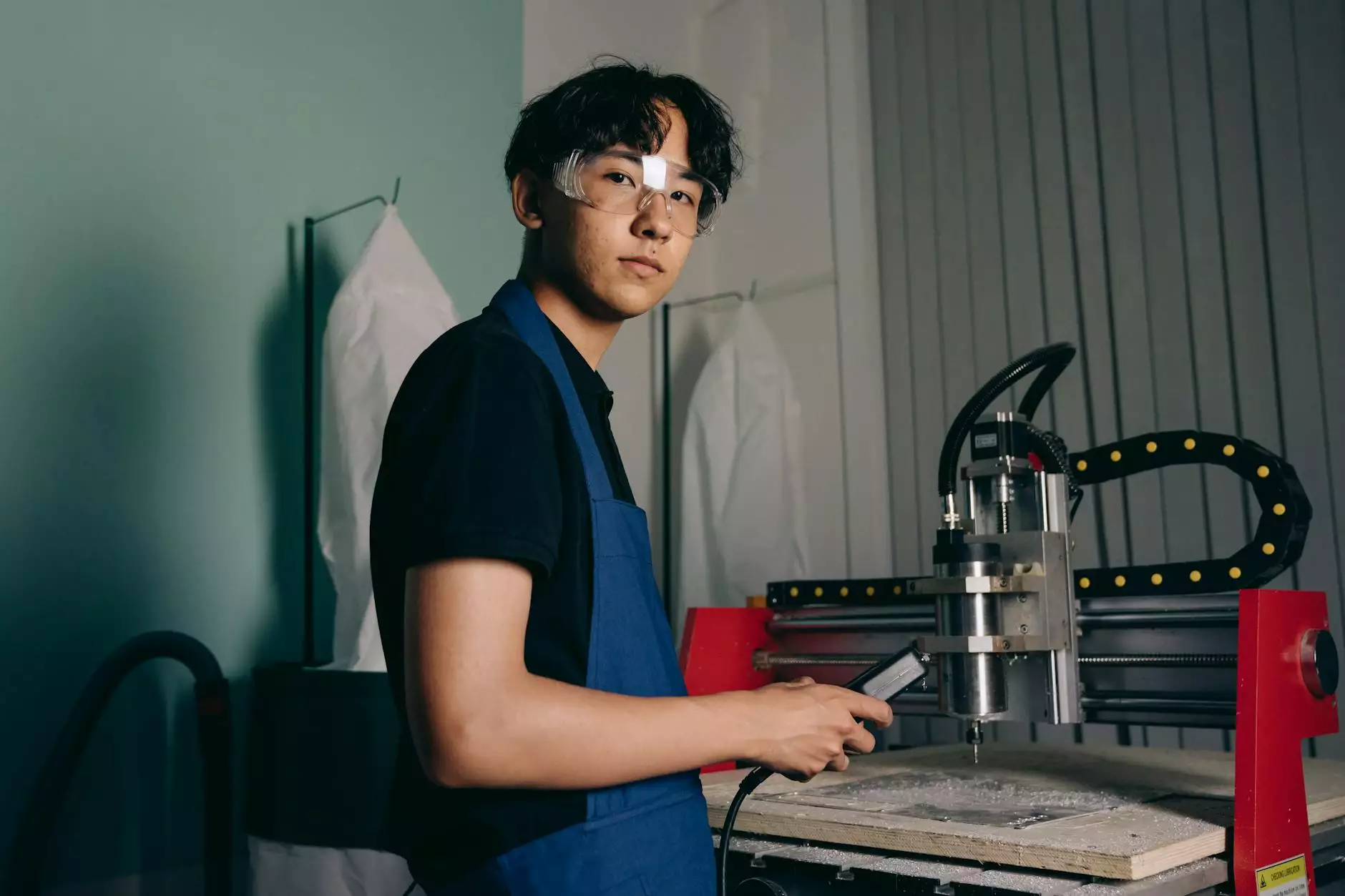
In today's fast-paced industrial landscape, CNC lathe factories have emerged as pivotal players in the realm of metal fabrication. With the increasing demand for precision, efficiency, and quality in manufacturing processes, these factories are spearheading advancements that are reshaping the industry. This comprehensive article explores the significance of CNC lathe factories, their technologies, and how they contribute to the success of businesses like DeepMould.net.
Understanding CNC Machining and Its Evolution
CNC, or Computer Numerical Control, is a revolutionary technology that automates machine tools through programmed commands. Originating in the 1950s, CNC machining has undergone profound evolution, transitioning from basic controls to sophisticated systems that now dominate various sectors of industry.
History of CNC Technology
- 1950s: The inception of CNC technology marked the shift from manual to automated machining.
- 1960s-70s: Introduction of computer systems that allowed for improved accuracy and repeatability in manufacturing.
- 1980s-90s: The rise of microprocessors revolutionized CNC machinery, promoting greater versatility.
- 2000s-Present: Integration of advanced software, 3D modeling, and real-time data analysis for enhanced production efficiency.
The evolution of CNC technology has led to the establishment of CNC lathe factories, which specialize in producing components with high precision and complex geometries that are critical in various applications ranging from automotive to aerospace.
The Functionality of CNC Lathes
CNC lathes are essential tools in metal fabrication, offering unparalleled capabilities in transforming raw materials into finished parts. Utilizing a rotating workpiece and a stationary cutting tool, CNC lathes enable:
Key Functions of CNC Lathes
- Turning: The primary function allows for the machining of cylindrical objects.
- Facing: The process of creating a flat surface on the workpiece.
- Drilling: Precision holes can be created with utmost accuracy.
- Threading: Capability to create internal and external threads on components.
The automation provided by CNC lathes streamlines production, reduces waste, and significantly lowers the potential for human error, enhancing the overall quality of the fabricated metal parts.
Advantages of CNC Lathe Factories
Choosing a CNC lathe factory for metal fabrication offers numerous advantages that contribute to businesses' competitive edge. Below are some of the key benefits:
1. Enhanced Precision
CNC (Computer Numerical Control) technology ensures that every component produced is made with an incredibly high degree of accuracy. This precision is vital for industries that rely on tight tolerances, such as aerospace, automotive, and medical devices.
2. Increased Efficiency
Automation leads to faster production cycles. CNC machines can operate continuously, reducing downtime and significantly increasing output without sacrificing quality.
3. Flexibility in Production
CNC lathes are versatile and can handle a wide array of materials, including metals, plastics, and composites. Their programmability allows for quick adjustments between different production runs, making them ideal for both large-scale manufacturing and custom fabrication.
4. Lower Labor Costs
With CNC technology taking over complex tasks traditionally performed by skilled laborers, businesses can reduce their labor costs. Factories can reallocate human resources to more strategic roles, enhancing productivity across the board.
5. Consistency and Quality Control
The automated nature of CNC machining ensures consistent quality across production batches. This reliability is crucial for industries where even minor defects can lead to significant setbacks.
Applications of CNC Lathes in Metal Fabrication
The diversity of applications for CNC lathes in metal fabrication exemplifies their importance across multiple industries. Here are some of the predominant sectors that benefit from the advancements of CNC lathe factories:
1. Automotive Industry
The automotive sector relies heavily on CNC lathes for producing various components, including engine parts, brackets, and transmission housings. The need for precise tolerances and consistent quality makes CNC lathes indispensable in this industry.
2. Aerospace
CNC machining plays a critical role in aerospace manufacturing due to the stringent safety and performance standards. Components like turbine blades, landing gear parts, and structural elements are often produced using CNC lathes.
3. Medical Devices
The production of medical devices and instruments requires exceptional accuracy, which can be achieved through CNC lathes. Components such as surgical instruments and implantable devices are often manufactured with this technology to meet rigorous health standards.
4. Energy Sector
In the energy industry, CNC lathes are used to create parts for power generation, including turbine components and valves. The ability to work with high-strength materials is critical in this field.
The Technology Behind CNC Lathes
Modern CNC lathes incorporate a combination of hardware and software that together facilitate high-quality machining processes. Understanding the technology involved provides insight into what makes CNC lathes so effective.
1. CNC Control Systems
The heart of any CNC lathe is its control system, which translates design blueprints into machine commands. Advanced controllers enhance process efficiency through features such as:
- Adaptive control: Adjusts machining parameters in real time to optimize performance.
- Tool path optimization: Maximizes efficiency and reduces production time.
2. Tooling and Fixtures
The selection of appropriate tooling is crucial for achieving the desired results. High-speed steel, carbide, and ceramic tools are common in CNC lathe factories, each serving specific functions to improve cutting efficiency and tool life.
3. CAD/CAM Integration
Computer-Aided Design (CAD) and Computer-Aided Manufacturing (CAM) systems work in tandem to enhance the machining process. CAD software is used to design parts, while CAM software generates the necessary instructions for the CNC machines, creating a seamless workflow from concept to production.
Challenges Facing CNC Lathe Factories
Despite the overwhelming advantages of CNC lathe factories, there are challenges that the industry faces:
1. High Initial Investment
The cost of CNC machinery and the integration of sophisticated software can be significant, which may deter smaller business owners from investing in this technology.
2. Skill Gap and Training
While CNC technology reduces the need for extensive manual skills, it does require a workforce skilled in programming and machine setup. Continuous training is necessary to keep pace with technological advancements.
3. Maintenance and Upgrades
CNC machines require regular maintenance to ensure optimal performance. Additionally, technological advancements mean that factories must periodically upgrade their equipment, adding to operational costs.
The Future of CNC Lathe Factories
The future of CNC lathe factories is bright and filled with opportunities as technology continues to evolve. Some trends include:
1. Technological Advancements
Emerging technologies such as Artificial Intelligence (AI) and the Internet of Things (IoT) are being integrated into CNC processes to optimize production and improve operational efficiency.
2. Customization and On-Demand Production
With the increase in consumer demand for customization, CNC lathe factories are adapting to produce bespoke solutions for a wide array of industries.
3. Sustainable Manufacturing Practices
CNC technology can contribute to more sustainable manufacturing practices by minimizing waste and enabling the recycling of materials, aligning with global trends towards eco-friendly production.
Conclusion
In conclusion, CNC lathe factories are at the forefront of modern metal fabrication, driving efficiency, precision, and innovation across multiple industries. As technology advances and the market evolves, these factories are poised to remain integral to the global manufacturing landscape. Embracing the benefits of CNC technology can position businesses like DeepMould.net as leaders in the industry, ensuring they deliver quality products that meet the ever-growing demands of their clientele.
By understanding the intricacies of CNC lathe operations, businesses can harness these capabilities to transform their production processes, enhance product quality, and ultimately achieve greater market success.