Understanding the Role of Tube Fittings Manufacturers in Industrial Applications
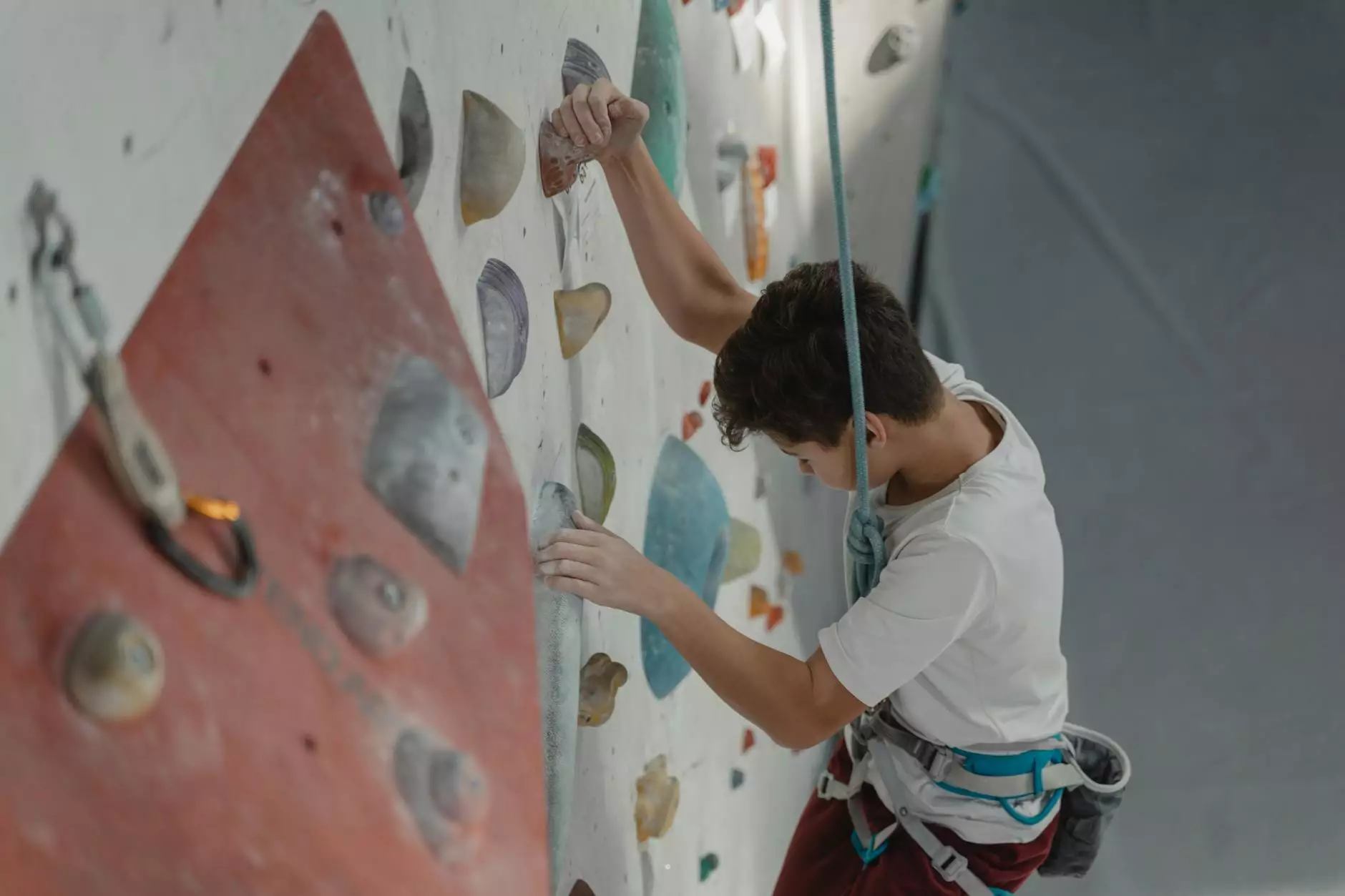
In the realm of industrial engineering, the significance of tube fittings manufacturers cannot be overstated. These manufacturers produce essential components that play a vital role in the functionality and safety of various systems. This article offers comprehensive insights into the diverse offerings of tube fittings and their critical applications across different industries.
What Are Tube Fittings?
Tube fittings are mechanical devices used to connect two or more tubes or pipes in fluid transportation systems. These components are integral to ensuring tight, leak-free connections, allowing for efficient and safe movement of fluids, gases, or slurries. Tube fittings come in various designs and materials, catering to a broad spectrum of applications.
Types of Tube Fittings
As one of the premier tube fittings manufacturers, we offer a wide array of products. Here’s a closer look at some of the main types:
- Ferrule Fittings: Known for their ability to create a strong, reliable seal, ferrule fittings are essential in high-pressure applications.
- Forged Pipe Fittings: These are manufactured through forging, ensuring exceptional strength and durability.
- Threaded Pipe Fittings: Designed for easy assembly, threaded fittings are used in a variety of piping applications.
- Flanges: Flanges are vital for connecting pipes, valves, and other equipment, providing a reliable connection point.
- Check Valves: These prevent backflow in a system, ensuring unidirectional flow of fluids.
- Ball Valves: Ideal for on/off control, these valves provide a tight seal and maximum flow efficiency.
- Needle Valves: Perfect for flow regulation, needle valves allow for precise control of fluid flow.
- Manifold Valves: Used for combining multiple fluid paths, these valves are essential for complex fluid systems.
- Double Ferrule Tube Fittings: These fittings enhance the leak-proofing of connections, making them ideal for high-pressure applications.
- Single Ferrule Tube Fittings: Offering ease of assembly, single ferrule fittings are effective for low-pressure lines.
- NPT Fittings: National Pipe Thread fittings ensure a secure threaded connection in piping systems.
Benefits of Choosing Quality Tube Fittings
Selecting high-quality tube fittings from reputable tube fittings manufacturers like Techtubes can significantly impact the performance of your industrial operations. Here are some of the benefits:
1. Enhanced Durability
Quality tube fittings are designed to withstand harsh environments, high pressures, and extreme temperatures. This durability ensures that your systems operate smoothly without frequent failures or replacements, leading to reduced maintenance costs and downtime.
2. Improved Safety
Leakage in fluid transport systems poses severe safety risks. High-quality fittings offer a secure, leak-free connection, mitigating risks and ensuring the safety of operations and personnel.
3. Efficiency and Performance
Using fittings that are specifically designed for your application enhances the efficiency and performance of your fluid transport systems. This is crucial for maintaining operational effectiveness and meeting production targets.
4. Custom Solutions
Many tube fittings manufacturers offer custom solutions tailored to specific needs. This flexibility allows for unique designs that fit particular industrial requirements, further enhancing performance.
The Manufacturing Process of Tube Fittings
Understanding the manufacturing process is essential for discerning the quality of tube fittings. Here’s how reputable manufacturers like Techtubes create these vital components:
1. Material Selection
The process begins with selecting the right materials, which can range from stainless steel, carbon steel, brass, to high-performance alloys. This selection depends on the intended application and environmental conditions.
2. Machining and Forming
After material selection, the materials are shaped through various machining techniques such as milling, turning, and forging. This stage ensures that the fittings conform to precise dimensions required for efficient operation.
3. Surface Treatment
Surface treatments, such as plating, coating, or polishing, enhance resistance to corrosion and wear, extending the lifespan of the fittings.
4. Quality Testing
All fittings undergo rigorous quality testing, including pressure tests and leak tests, ensuring they meet industry standards and client specifications.
Applications of Tube Fittings in Various Industries
Tube fittings are utilized across numerous sectors, each leveraging the reliability and efficiency of these components:
1. Oil and Gas Industry
In the oil and gas sector, tube fittings are crucial for managing high-pressure systems, ensuring safe and efficient transportation of crude oil and natural gas. Their ability to withstand harsh conditions makes them indispensable.
2. Chemical Processing
For chemical processing plants, tube fittings ensure the safe transfer of chemicals, which often requires special materials resistant to corrosion and chemical reactions. High-quality fittings help in maintaining system integrity.
3. Pharmaceuticals
The pharmaceutical industry relies on tube fittings to maintain sterility and safety in drug manufacturing processes. Fittings that comply with sanitary standards are essential in this critical sector.
4. Food and Beverage
In the food and beverage industry, tube fittings must meet stringent health and safety regulations. They are designed to prevent contamination and ensure a smooth, efficient production process.
5. Aerospace
Aerospace applications demand lightweight and high-strength materials. Tube fittings used in aircraft systems provide reliability under extreme conditions, contributing to overall safety and efficiency.
Choosing the Right Tube Fittings Manufacturer
When selecting a manufacturer for your tube fittings, consider the following factors:
- Experience: Look for manufacturers with a proven track record in the industry.
- Reputation: Research customer reviews and testimonials to gauge reliability and quality.
- Certifications: Ensure they comply with industry standards and regulations.
- Customization: Check if they offer custom solutions to meet your specific needs.
- Support and Service: Consider the level of customer support and technical assistance they offer.
Conclusion
The role of tube fittings manufacturers is pivotal in ensuring the performance, safety, and efficiency of industrial systems. By choosing high-quality fittings from established brands like Techtubes, businesses can enhance their operations and minimize risks associated with fluid transport. With the right selection and understanding of the applications, industries can benefit significantly from the advancements in tube fitting technology.
For more information about our products, including Ferrule Fittings, Forged Pipe Fittings, Check Valves, Ball Valves, and more, visit us at Techtubes.in.