Understanding Plastic Mold Tools: A Comprehensive Guide for Metal Fabricators
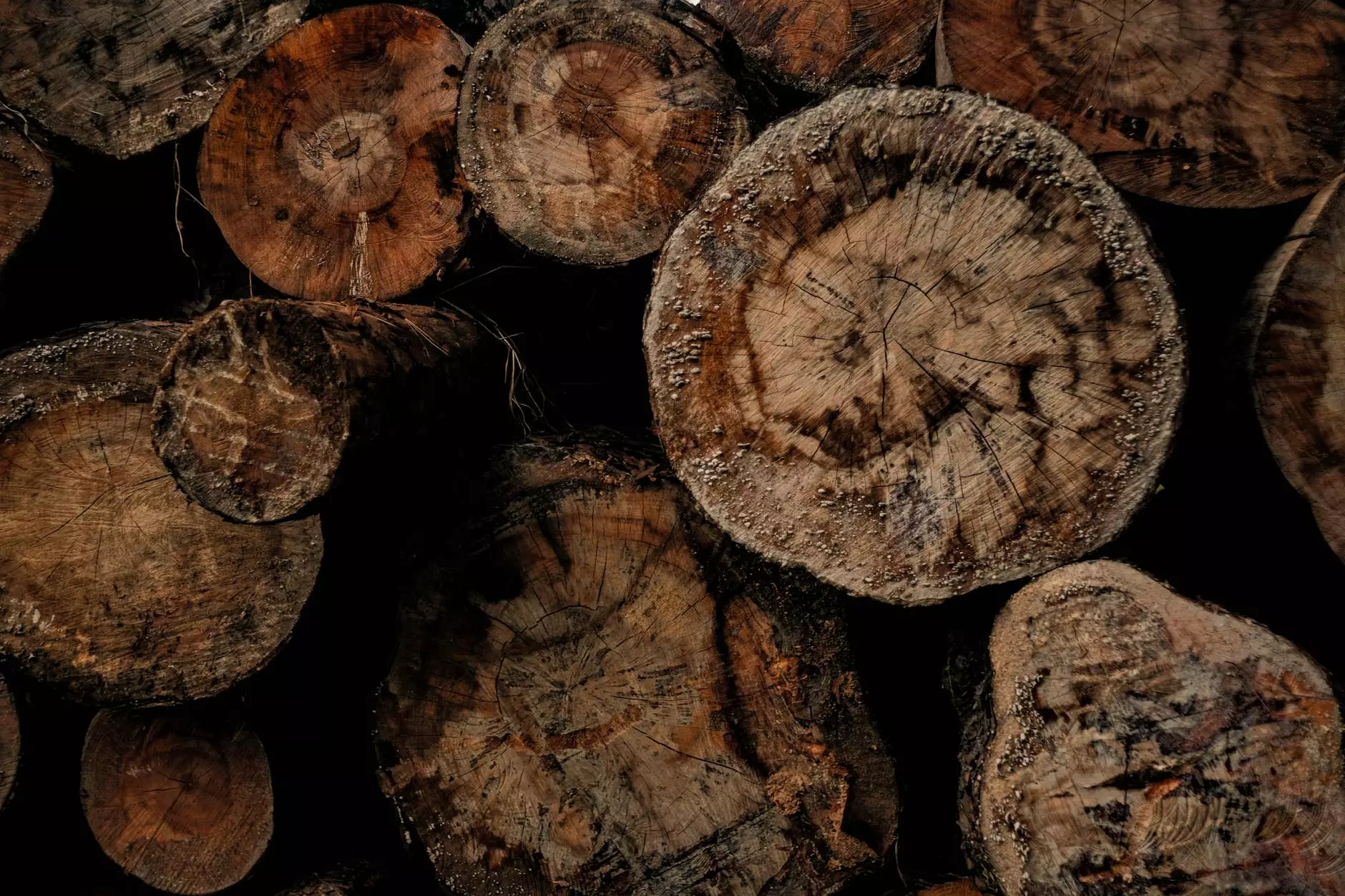
In the world of manufacturing, the efficiency and effectiveness of your processes are paramount. One critical aspect that underpins success in this arena is the use of plastic mold tools. These tools are indispensable in the production of high-quality components and products, providing the precision and reliability that every metal fabricator seeks.
What Are Plastic Mold Tools?
Plastic mold tools are specialized equipment used to form and shape plastic materials into desired configurations. They are essential in processes such as injection molding, blow molding, and compression molding. These tools allow for the creation of intricate designs while ensuring consistency and durability across productions.
The Components of Plastic Mold Tools
Understanding the components of plastic mold tools can give insights into their operation and efficiency. The key components include:
- Mold Base: The sturdy framework that holds the mold components together.
- Cavities: The hollow sections where the molten plastic is injected to form the shape.
- Core: The part of the mold that shapes the interior details of the product.
- Cooling Channels: Designed to maintain the optimal temperature of the mold during operation.
- Ejection System: Mechanisms that help release the finished product from the mold.
Applications of Plastic Mold Tools in Metal Fabrication
Plastic mold tools are not solely for plastic items; their applications extend to various sectors, driving innovation in metal fabrication. Some notable applications include:
- Prototyping: Quickly create prototypes for testing before mass production.
- Complex Designs: Fabricate intricate parts that are challenging to produce using traditional machining.
- Producing Consistent Components: Achieve uniformity in parts, critical for high-quality manufacturing.
- Cost Efficiency: Reduce production costs through efficient use of materials and minimized waste.
Advantages of Using Plastic Mold Tools
The advantages of incorporating plastic mold tools into your manufacturing process are numerous. Consider the following benefits:
1. Precision and Accuracy
Plastic mold tools allow for high precision in designing components, resulting in perfect fitting parts that minimize the need for secondary operations.
2. Enhanced Production Speed
By automating the molding process, manufacturers can significantly reduce production time, boosting overall efficiency while meeting demand.
3. Versatility
These tools can accommodate a wide range of materials and applications, making them adaptable for various industries, including automotive, medical, and consumer products.
4. Cost Savings
While the initial investment may be considerable, the long-term savings related to reduced waste, lower energy costs, and decreased labor can be substantial.
Choosing the Right Plastic Mold Tools for Your Business
When selecting plastic mold tools, it is crucial to consider various factors to ensure the best fit for your business needs:
1. Type of Material
Identify the type of materials you will be working with, as they influence the mold design and construction.
2. Production Volume
Understanding the volume of parts needed helps in determining whether to invest in a prototype mold or a more durable production mold.
3. Complexity of Design
The complexity of the parts you aim to produce will dictate the intricacies of the mold itself.
4. Budget Constraints
Establishing a budget allows you to narrow down your options while still meeting design and production needs.
Future Trends in Plastic Mold Tools
The industry continues to evolve, and the trends shaping the future of plastic mold tools are promising:
1. Smart Manufacturing
The integration of IoT and AI in the manufacturing process is transforming traditional molding operations, enabling predictive maintenance and enhanced efficiency.
2. Sustainability
As companies aim to reduce their carbon footprint, the development of eco-friendly materials and processes for plastic mold tools is emerging as a key trend.
3. Advanced Materials
Research into high-performance materials will continue to expand, leading to stronger and lighter molds that withstand more rigorous conditions and pressures.
4. Customization
Businesses will increasingly demand tailor-made solutions, pushing manufacturers to innovate and create molds that meet specific needs and applications.
Conclusion: Investing in Quality Plastic Mold Tools
Investing in high-quality plastic mold tools is essential for any metal fabricator looking to stay competitive in today’s market. By understanding their functionality, applications, and advantages, you can make informed decisions that enhance your production capabilities. As industry demands grow, so does the necessity for precision, efficiency, and adaptability—which is exactly what plastic mold tools offer.
To stay ahead, explore the offerings on deepmould.net and discover how superior plastic mold tools can transform your manufacturing processes, ensuring you not only meet but exceed the expectations of your clients.