The Revolutionary Rise of Forged Carbon Car Parts
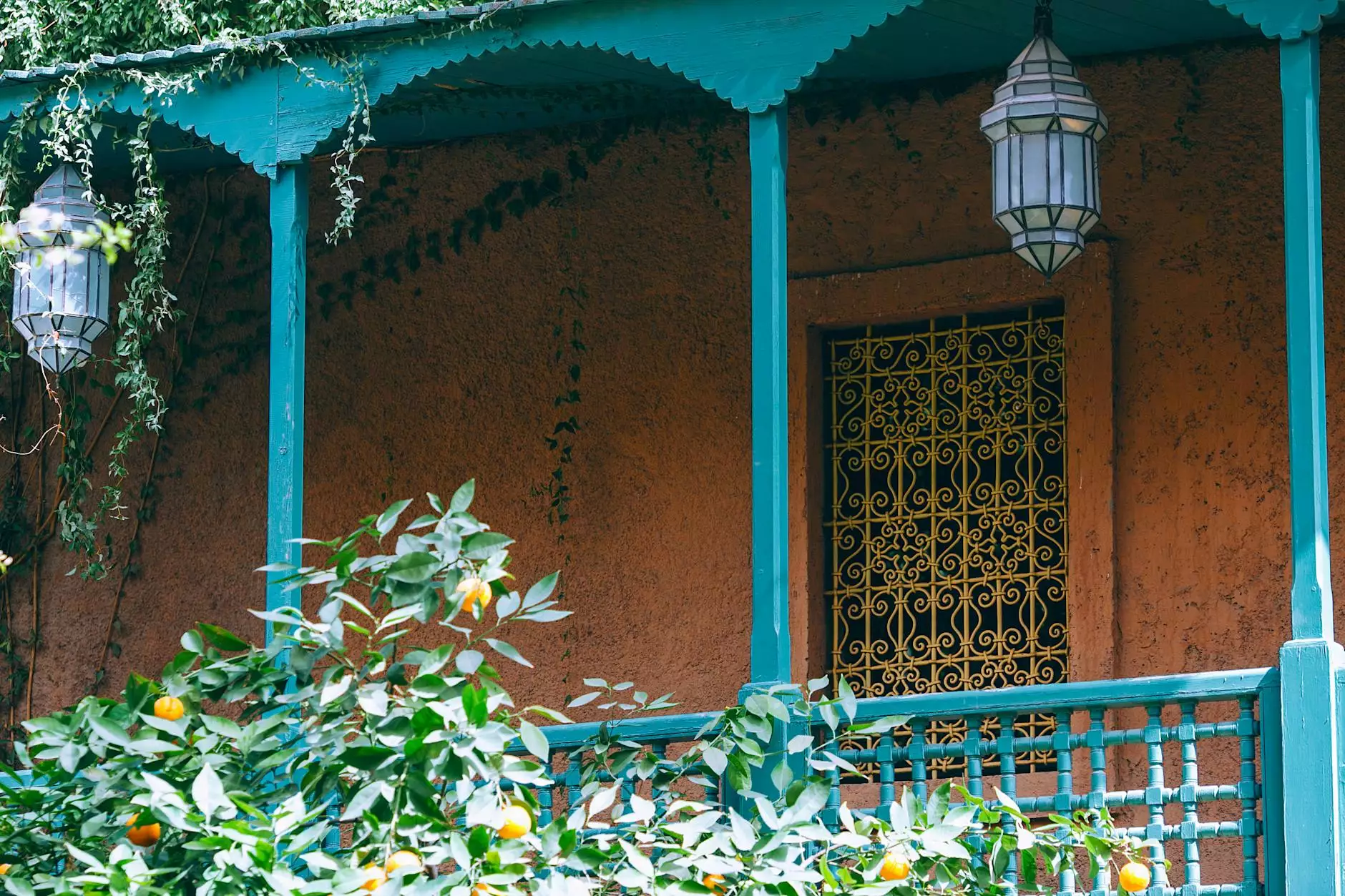
Forged carbon car parts are at the forefront of innovation in the automotive industry, revolutionizing the way we think about performance, durability, and aesthetic appeal in vehicles. As industries evolve, so do the materials that manufacturers use to build the cars we drive. This article delves into the benefits, manufacturing processes, and the future of forged carbon car parts, illustrating their significance in today's automotive landscape.
Understanding Forged Carbon
Before we dive deep into the advantages and applications of forged carbon car parts, it is essential to understand what forged carbon is and why it has become a game-changer in the automotive field.
What is Forged Carbon?
Forged carbon is an advanced composite material made from short strands of carbon fiber that are combined with a resin and then compressed and heated to form a solid, lightweight structure. Unlike traditional carbon fiber, which is often used in long, unbroken sheets, forged carbon utilizes a more versatile approach by harnessing the properties of carbon fibers and integrating them into a matrix that can be molded into various shapes.
Key Benefits of Forged Carbon
- Weight Reduction: One of the most significant advantages of forged carbon car parts is their lightweight nature. This reduction in weight translates into better fuel efficiency and improved handling.
- Superior Strength: Forged carbon exhibits exceptional tensile strength, which allows it to withstand greater forces and impacts compared to traditional materials such as aluminum and steel.
- Enhanced Design Flexibility: The manufacturing process allows designers to create complex shapes and unique aesthetics that are not feasible with conventional materials.
- Corrosion Resistance: Unlike metals, forged carbon does not corrode. This property gives automotive manufacturers the advantage of longevity and durability.
- Cost-Effective Production: With advances in technology, the production of forged carbon can be more cost-effective than traditional carbon fiber methods, making it accessible to a broader range of applications.
Applications of Forged Carbon in Automotive Industry
The use of forged carbon car parts is becoming increasingly prevalent across various segments of the automotive industry. From high-performance supercars to everyday vehicles, forged carbon finds its place in numerous components:
1. Aerodynamic Components
Aerodynamics play a crucial role in vehicle performance. Forged carbon is used to create lightweight spoilers, splitters, and diffusers that enhance the car's aerodynamic efficiency while contributing to weight reduction.
2. Structural Parts
In high-performance vehicles, structural integrity is paramount. Forged carbon components such as chassis supports and frame elements provide the necessary strength while keeping the weight low, which is vital during high-speed maneuvers.
3. Interior Design
The aesthetic appeal of forged carbon is attracting the attention of luxury car manufacturers. Interior trims, dashboard components, and steering wheel designs utilizing forged carbon offer a modern and appealing look that resonates with consumers looking for customization and prestige.
4. Engine Components
Forged carbon parts are being explored for use in engine components due to their high-strength characteristics and resistance to heat. Cam covers, intake manifold parts, and other engine accessories can benefit significantly from forged carbon technology.
Manufacturing Processes Behind Forged Carbon
The production of forged carbon car parts involves cutting-edge manufacturing techniques that ensure precision and quality. Here’s a closer look at the processes involved:
1. Material Preparation
The process begins with the careful selection of short carbon fibers, which are mixed with a polymer resin to create a composite material. The properties of the resin can be adjusted to meet specific performance requirements.
2. Forging
The mixed material is then placed into a forge where it undergoes high pressure and heat treatment. This stage is crucial as it compacts the material into a denser structure, enhancing its mechanical properties.
3. Molding and Cooling
Once forged, the material is placed into molds to form the desired shapes. After cooling, the forged carbon continues to harden, leading to a final product that is both lightweight and incredibly strong.
4. Surface Finishing
After molding, the parts undergo surface finishing processes to ensure a sleek appearance and eliminate any imperfections. This step is particularly important for components that will be visible in the vehicle's interior.
Future Trends in Forged Carbon Technology
The future of forged carbon car parts appears bright, driven by continuous innovations and heightened consumer demand for sustainable and lightweight materials. Below are some trends to watch for:
1. Increased Adoption in Mass Production
As the technology matures and costs decrease, manufacturers are expected to adopt forged carbon for mass-produced vehicles, leading to broader availability and applications.
2. Sustainability Focus
With the automotive industry's shift towards sustainability, the development of bio-based resins for forged carbon presents an opportunity to create environmentally friendly components without compromising performance.
3. Integration with Smart Technologies
As vehicles become more advanced with smart technologies, the integration of forged carbon with sensors and other electronic devices could lead to smarter, lighter, and more efficient vehicles.
4. Customization and Personalization
Consumers are increasingly looking for personalized vehicles. Forged carbon offers a wide range of customization options for car enthusiasts, allowing them to upgrade performance parts and stylish interiors without excess weight.
Conclusion
In conclusion, forged carbon car parts are poised to become a cornerstone of modern automotive design and engineering. With their myriad benefits, including weight reduction, strength, and design flexibility, forged carbon materials are not just a trend but a vital component of the future of the automotive industry. As more manufacturers recognize their advantages, the landscape of vehicle production will undoubtedly evolve, leading to better, faster, and more sustainable cars. At customclass.net, we are committed to staying at the forefront of these innovations, ensuring our customers benefit from the latest advancements in automotive technology.