Understanding the Role and Importance of Gear Mould Manufacturers
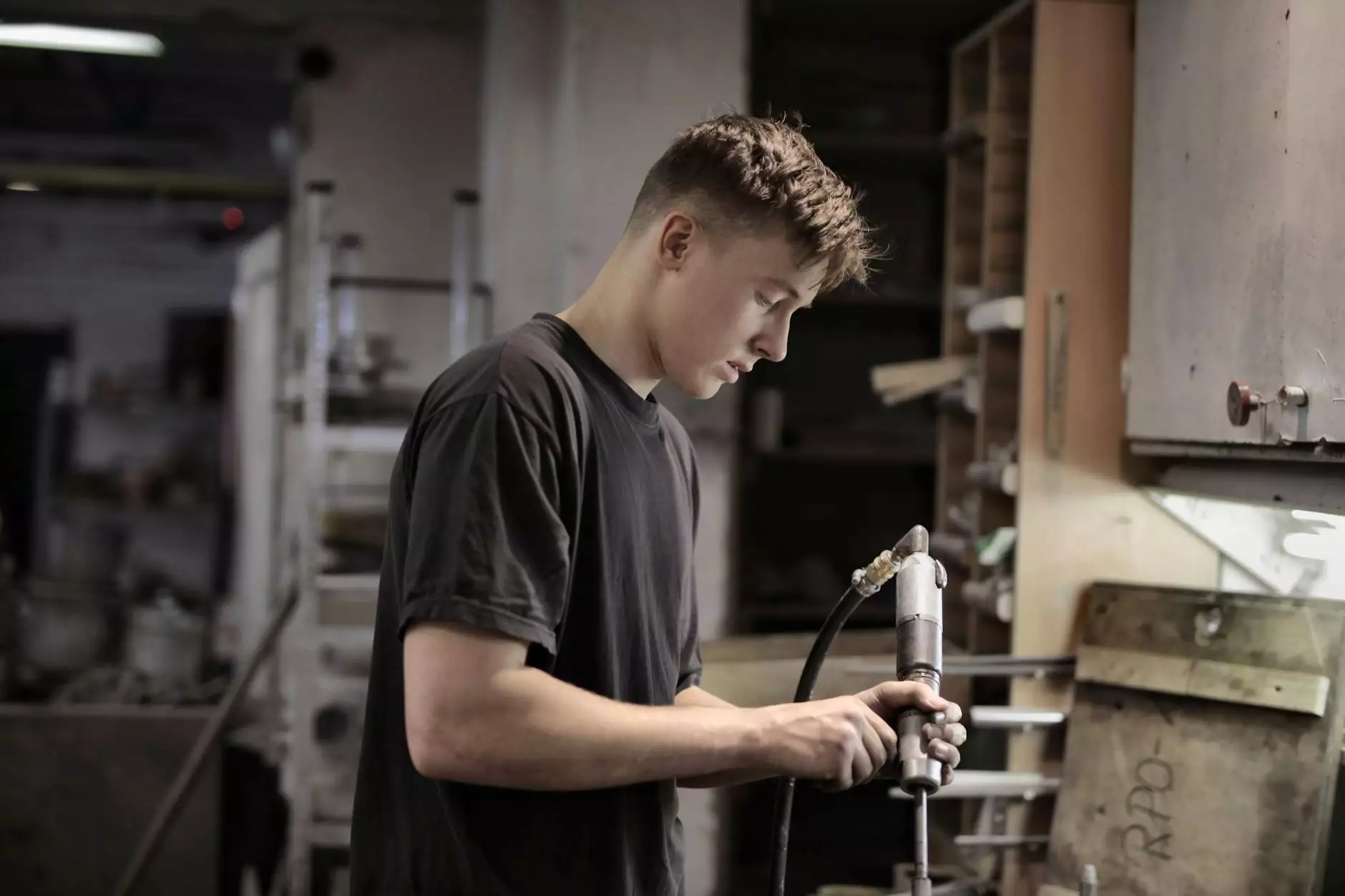
In today's competitive industrial landscape, the demand for high-quality precision parts has surged, especially in the automotive and machinery sectors. Gear mould manufacturers play a pivotal role in this ecosystem by providing the essential tools and molds needed to produce intricate gear components. This article delves into the world of gear mould manufacturing, highlighting its methodologies, benefits, and the significance of selecting the right manufacturer for your business needs.
The Importance of Gear Moulds in Manufacturing
Gear moulds are essential in the production of high-precision gears that are used across various industries. These moulds are crafted to ensure that each gear meets stringent quality standards and specifications. The process involves a complex interplay of design, material selection, and precision engineering.
Types of Gears and Their Applications
Before delving deeper into the role of gear mould manufacturers, it is crucial to understand the types of gears commonly produced and their applications:
- Spur Gears: These are the simplest type of gear, which are characterized by their straight teeth and are used in various machines for their efficiency.
- Helical Gears: Unlike spur gears, helical gears have angled teeth, providing smoother and quieter operation, making them ideal for automotive applications.
- Bevel Gears: Used to change the direction of rotation, bevel gears are prevalent in applications where shafts must be connected at an angle.
- Worm Gears: Known for their unique ability to provide high torque reduction with minimal space, these gears find use in elevators and conveyor systems.
- Planetary Gears: These are crucial in automatic transmissions, where they allow for speed variation and torque multiplication.
How Gear Mould Manufacturers Operate
Gear mould manufacturers utilize advanced technologies and techniques to produce precise and durable moulds. The process includes:
1. Design and Engineering
The journey begins with intricate design and engineering. Using CAD (Computer-Aided Design) software, manufacturers create detailed blueprints of the gears and moulds. This stage is critical as it lays the foundation for the entire production process.
2. Material Selection
The choice of material is paramount. Common materials for gear moulds include:
- Steel: Renowned for its strength and durability, steel is often used in high-stress applications.
- Aluminum: Lightweight and corrosion-resistant, aluminum is suitable for less demanding environments.
- Plastic: Ideal for low-load applications, plastic gear moulds are economical and versatile.
3. Mould Fabrication
Once the designs are finalized and materials selected, the actual mould fabrication begins. This involves several techniques, including:
- CNC Machining: Automated machines are employed to carve out the precise shapes required for the mould.
- EDM (Electrical Discharge Machining): This technique ensures high accuracy for complex geometries.
- 3D Printing: Gaining popularity for rapid prototyping, 3D printing allows for quick production of certain mould components.
4. Quality Control
Quality assurance is critical in the gear mould manufacturing process. Manufacturers implement stringent quality control measures to ensure that every mould meets required specifications. This involves dimensional checks, material tests, and functional testing.
Benefits of Partnering with Professional Gear Mould Manufacturers
Engaging with proficient gear mould manufacturers brings several advantages to a business, including:
1. Precision and Quality
Professional manufacturers invest in advanced technology and skilled labor, ensuring that every gear produced meets high precision and quality standards. This leads to more efficient and reliable machinery.
2. Cost-Effectiveness
While partnering with a renowned manufacturer might involve higher initial costs, the long-term savings from improved efficiency and reduced downtime often outweigh these expenses.
3. Customization
Many manufacturers offer bespoke solutions tailored to specific requirements. This flexibility allows businesses to obtain exactly what they need, enhancing productivity and performance.
4. Expertise and Support
When you work with established gear mould manufacturers, you benefit from their extensive experience and support. They can provide valuable insights and assistance throughout the production process.
Choosing the Right Gear Mould Manufacturer
Selecting the right manufacturer is crucial for the success of your project. Consider the following factors:
1. Experience and Reputation
Research the background of the manufacturer and their standing in the industry. A company with a proven track record is likely to possess the expertise needed to deliver quality moulds.
2. Technology and Equipment
The manufacturer should utilize state-of-the-art technology to ensure precision and efficiency. Ask about their machinery and software capabilities.
3. Portfolio and References
Review their past work, particularly in your industry. Request references to gain insights into their reliability and quality.
4. Customer Service
Reliable customer service is essential. Ensure that the manufacturer is responsive and willing to assist you throughout the process.
The Future of Gear Mould Manufacturing
As technology advances, the landscape of gear mould manufacturing is evolving. Innovations such as additive manufacturing and smart manufacturing are paving the way for more efficient production processes.
With the rise of Industry 4.0, gear mould manufacturers are increasingly integrating IoT (Internet of Things) technology, enabling real-time monitoring and management of production systems. This not only enhances the quality of the moulds produced but also significantly reduces lead times.
Conclusion
In conclusion, gear mould manufacturers are at the heart of the production process for high-precision gears essential in various industries. Their expertise, advanced technologies, and commitment to quality play a vital role in ensuring that businesses can operate efficiently and effectively. By choosing a reputable manufacturer, companies can harness the benefits of tailored solutions, cost savings, and superior product quality. The future holds exciting prospects for this industry, with continuous improvements and innovations leading the way. Developing strong partnerships with these manufacturers will undoubtedly pave the path for success in today’s complex manufacturing environment.